Optical Bonding Facilities
Data Image has an in-house production line for optical bonding - a method with which to provide increased visibility and durability to LCD monitors. Producing optical bonding in-house allows Data Image to continue to meet the needs of specialty markets while ensuring each product maintains high quality standards.
Improved readability in sunlight
Reduce reflection
Enhance Ruggedness and durability
Prevents condensation or fog on the display
Core Technology
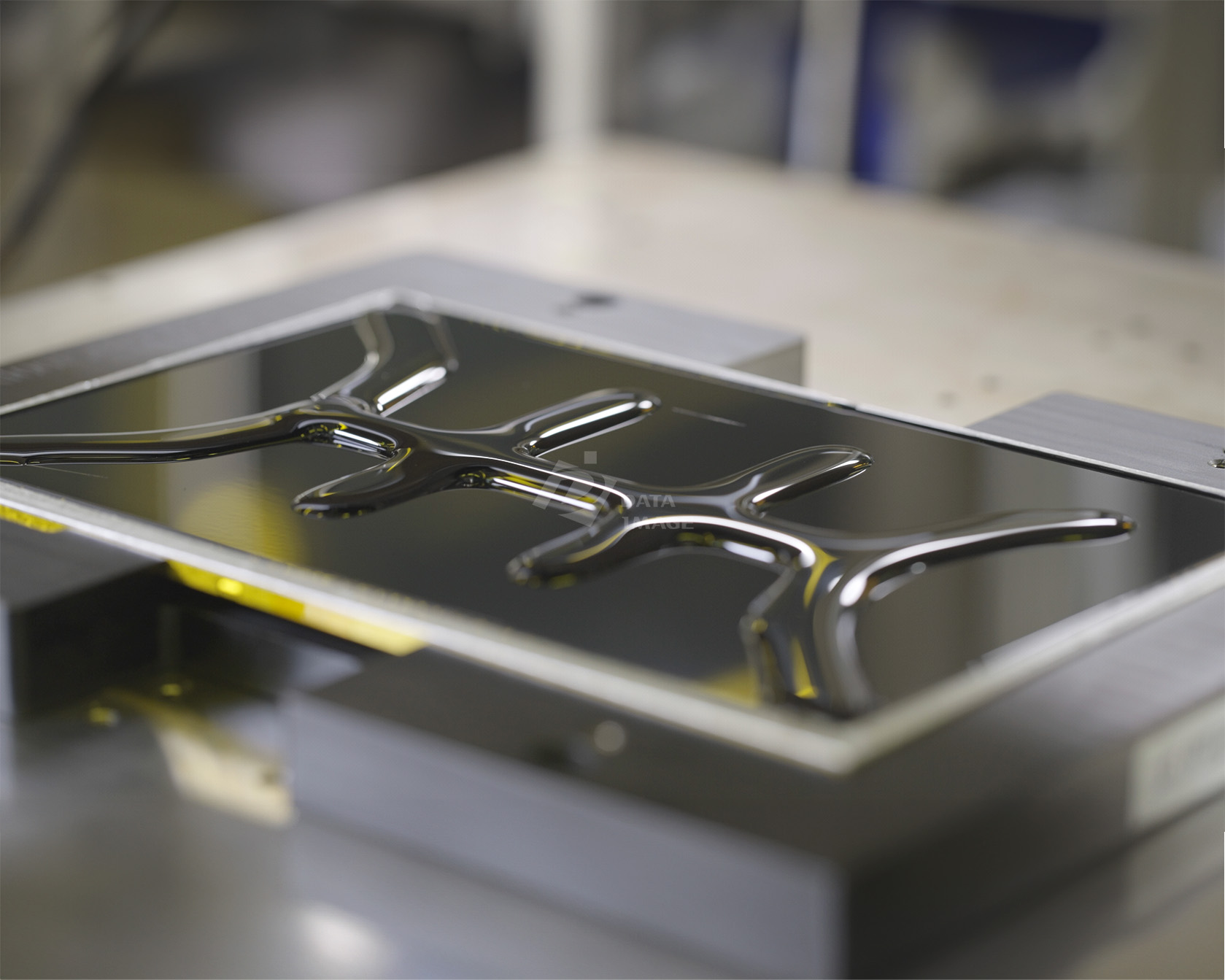
Optical Bonding
Basically, different methods and materials are used for optical bonding. Optical bonding can be carried out with silicone, polyurethane, epoxy resin and acrylate. There are 1-component systems as well as multi-component systems. The bonding material is crosslinked by mixing, heating or UV exposure. It is possible to apply the material in a liquid state to the components or dry in a precisely fitting form. If no liquid material is used, it is also called dry bonding. As with all adhesives, it is not only the choice of material that is decisive for optimum durability in optical bonding, it is also important to ensure good bonding to the surface of the components. At Data Image a special pre-treatment of the displays is carried out. The joining partners are pre-treated for the subsequent bonding process in a two-stage process. This means that even difficult display surfaces can be processed optimally.

Dry Bonding
In dry bonding, the bonding material is cut to the size of the visible display surface and the air gap is filled homogeneously with it. There is a choice of several bonding materials in different thicknesses and consistencies, which are selected on the basis of the displays and the specifications of the application. Displays have different heights of metal frames depending on the model and diagonal. The optimum material thickness is determined on the basis of the displays. The front glass with touch and display are joined together under vacuum in the bonding machine.

Wet Bonding
Unlike most displays, those used in automotive, marine interiors endure harsh environmental conditions, including extreme temperatures, high humidity, and prolonged UV exposure. They consequently demand more robust adhesive materials that still support simple, cost-effective processing.

OCA
OCA is a simpler, faster and more cost-effective process, still offering good durability and readability.
By applying this process, the air gap is eliminated and therefor the reflective index is reduced and brightness of the display increased, resulting in enhanced visibility.

OCR
OCR is the most durable of these methods, able to best withstand impact, shock and vibration. It offers the best readability, especially in sunlight, since it is best at eliminating internal reflections.
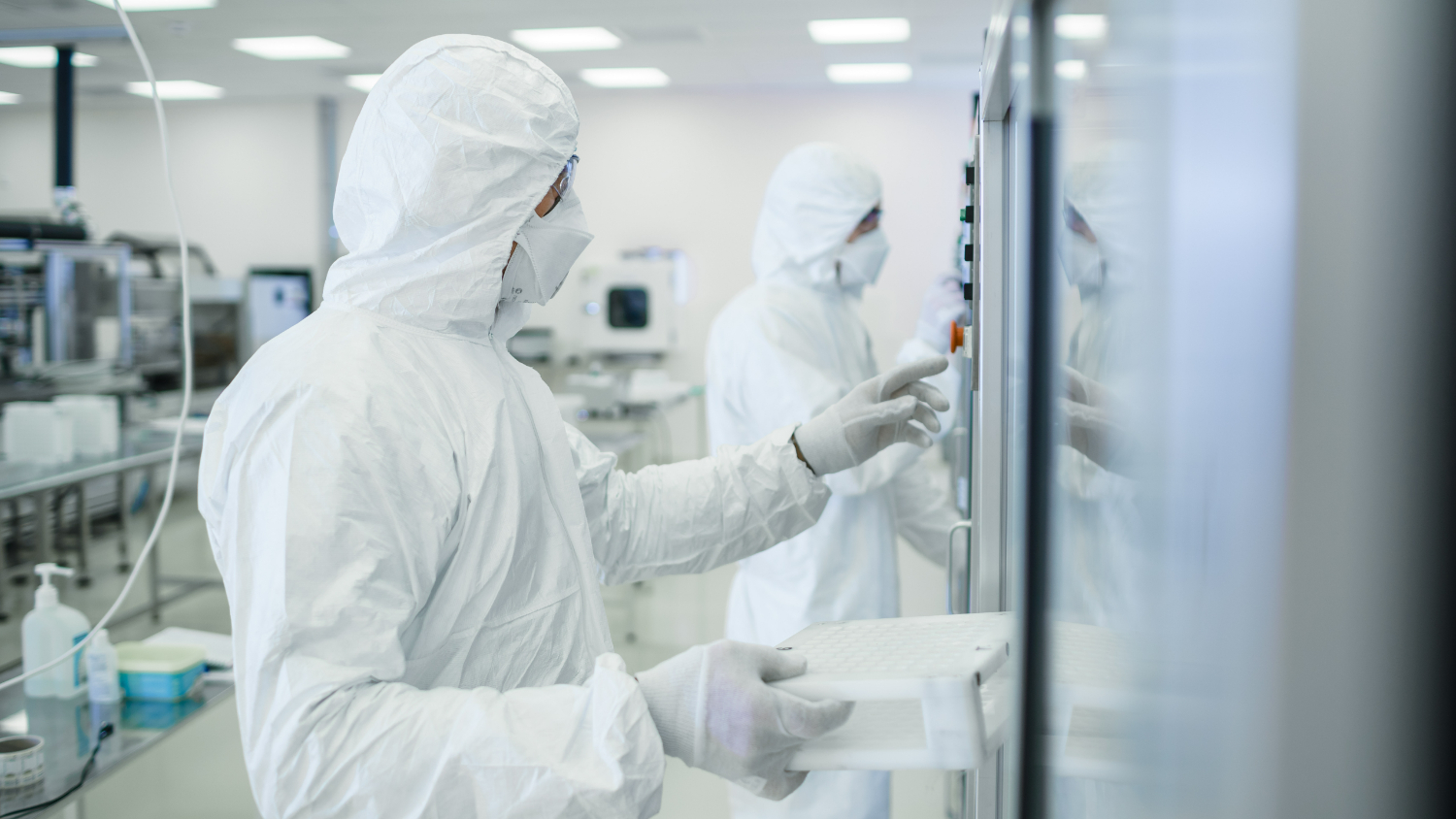
Which optical bonding process is suitable?
There are several technologies available for optical bonding of displays. The optimal process depends on the choice of components, system integration and application requirements.
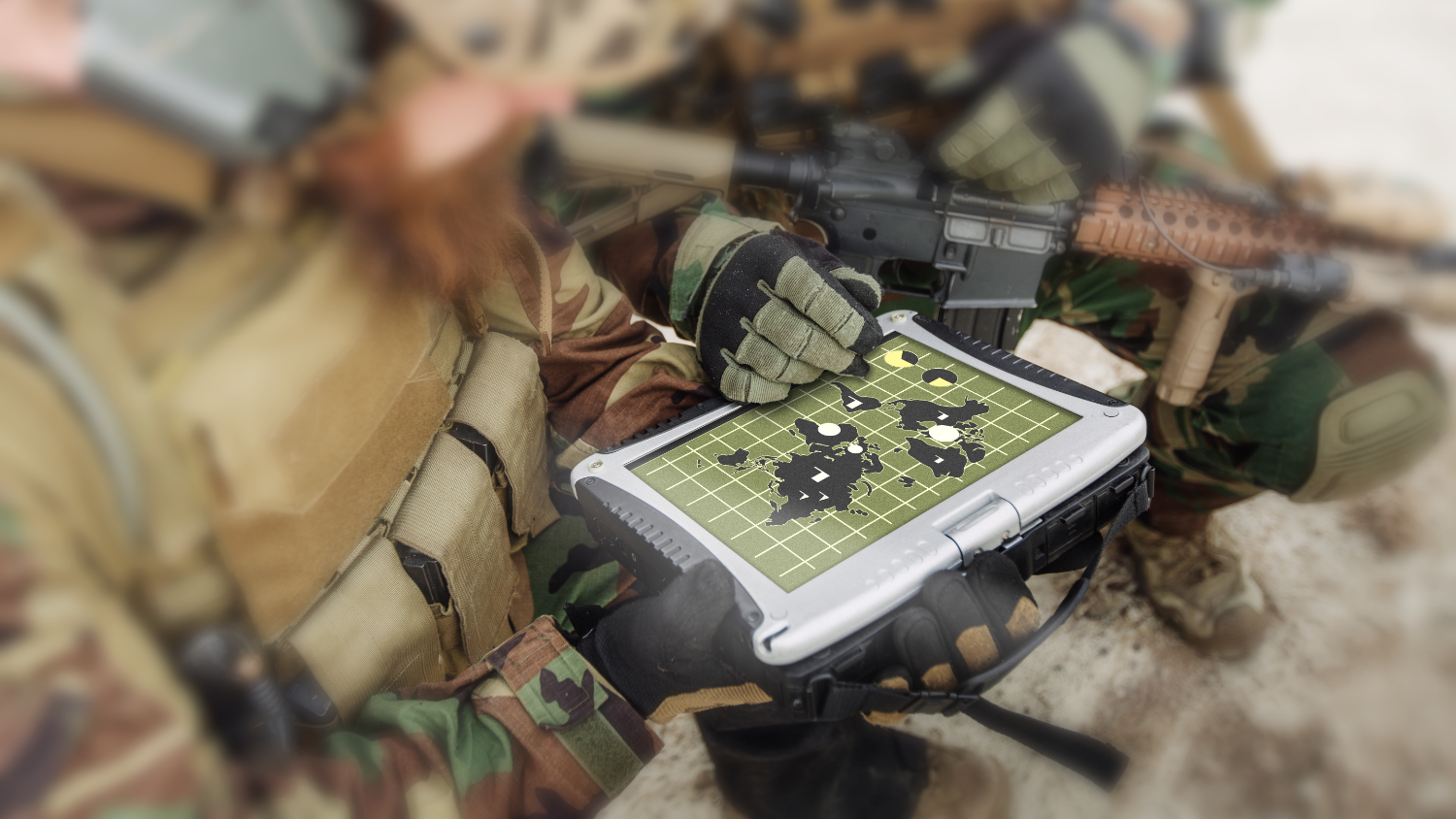
Increase product durability and performance
Specialized process enabling LCD assemblies to endure hostile and demanding environmentsHigh Altitude Pressures
Extended Temperatures
Heavy Shock and Vibration
Condensation and Moisture Prevention
Removes air gap between all bonded surfaces to eliminate any potential for condensation